Environmental, Health and Safety (EHS) Management and Audit
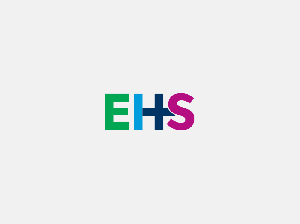
The practice of companies auditing their environmental, health and safety (EHS) began in the 1970’s, almost contemporaneously with the enactment of OSHA. Around that time, the environmental issue was gaining ground in the corporate circles of the West with the governments and other agencies pitching in with their efforts to create greater awareness of the impact of business activities on the environment. As a result, the thinking that the top management of an organization needs to be viewing this issue more seriously started to develop and got ingrained over the years.

As a result of various legislations on the issue of environmental safety; the role of the Board of Governors became central in ensuring this aspect of the business. Environmental health and safety was no longer something that needed to be administered superficially, but in formal and designated ways, more specifically in the form of an audit. In order to incentivize corporate entities to implement environmental health and safety (EHS) management and audit; the trend started moving towards making these activities carry value addition to the organization.
Environmental health and safety management and audit is now a more formalized activity that needs to be carried out in a proper, set and well-defined manner. The processes that go into the EHS management and audit are clearly laid out in the form of standards such as the ISO 14001 standard, which is essentially an Environmental Management System (EMS) audit. To strengthen and enrich the audit activity and round it better; a few related and parallel standards such as the relevant parts of the 9000 family of standards, which deals with quality management, and 18000 series audits can be carried out with ease to supplement the environmental, health and safety audit.

Environmental health and safety (EHS) management and audit have now evolved into being a practice that is coupled with and fused into many business-related activities. The practice now is to make an environmental health and safety management and audit an inseparable part of the Quality Management System. Environmental health and safety (EHS) management and audit audits are now a sure means to ensure that the organization has a reputation for corporate social responsibility by implementing this audit.

Click to Continue Reading
Labels: EHS, Environmental, environmental health, Health and Safety, Management and Audit, safety management, safety management and audit